This cup holder has been specifically designed and made for an electric wheelchair user. I had already made a cup holder for an older wheelchair, but it would not fit the new wheelchair.

Using a mix of CNC and manual machines I started out with a piece of 12mm thick aluminium plate, then drew the basic cup holder shape In Vectric V Carve to produce the necessary toolpaths.
A 6mm end mill slowly cut out the 10mm deep pocket and the outer profile.

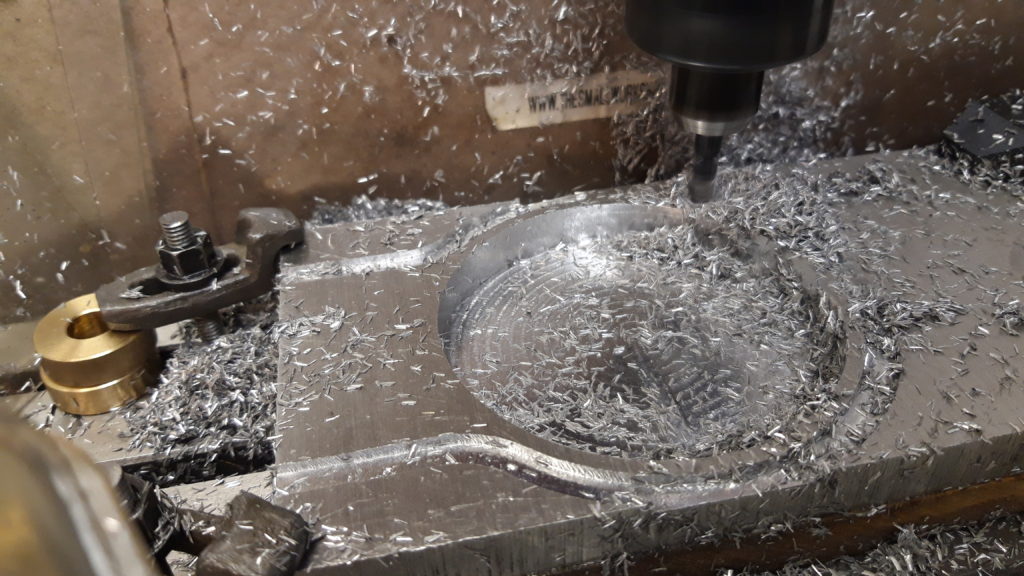
With the main cup holder shape cut out, I took a piece of 18mm square aluminium and milled out the hinge bracket.

A slot was cut into the main cup holder shape to accept the hinge bracket, this needed some filing to make sure both parts could hinge properly.
Then a 4mm diameter hole was drilled through both the cup holder and hinge.

A special 4mm diameter hinge pin was made on the lathe, it has a small lozenge shaped head which will fit into a recess in the bracket, this acts as a anti turn device when the nut is tightened up.
To make the cup holder stay in the upright position, I machined a slot in the hinge bracket to accept three small magnets which were glued into place. A smaller slot was milled into the cup holder to accept a small piece of mild steel bar, again glued into place. When filed down to a smooth surface the magnet and steel strip lined up perfectly to keep the cup holder upright when not in use.


After few more test fits and filing sessions to get the fit right, making a keep plate for the two M6 cap head screws, and a final test assembly it was nearly time to paint it.
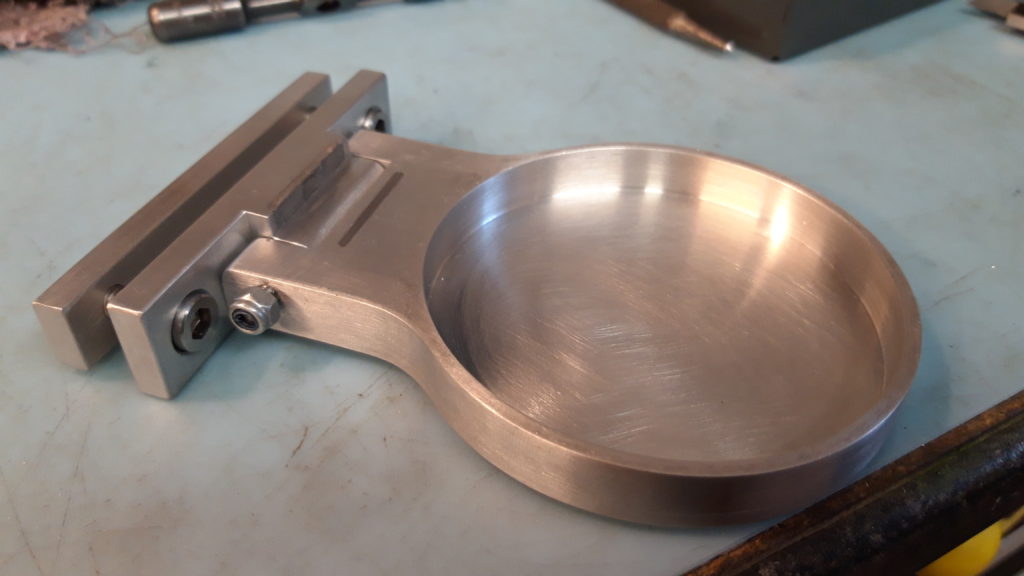
Painting was by using car spray paint and undercoat. The end result is petty good for me!

The keep plate slides into a ‘Tee’ slot on the wheelchair frame, and is held securely by the M6 screws. The magnets do a good job of holding it out of the way when not in use, but it is easy to drop the cup holder down to use it. And in a test the cup holder stays in the upright position even when going over bumpy ground.
Overall a very nice project which will definitely be used.
